Satisfied clients are fundamental for a business’s growth. For a company to enjoy repeat business from its customers, it must be able to deliver high-quality products through quick and efficient means. The latest industry reports indicate that after factors such as product price and convenience, shipping cost and wait time is one of the top considerations for customers when making a purchase.
It’s no surprise then that top businesses around the world recognize the importance of an efficient, streamlined supply chain and are willing to invest to achieve this. In Saudi Arabia, the logistics and warehousing market is showing a steady growth rate and is expected to garner revenue amounting to more than USD 17.5 billion by 2023. Indeed, with the rise of e-commerce across the kingdom, more businesses are outsourcing their warehouse management than ever before.
What is warehousing?
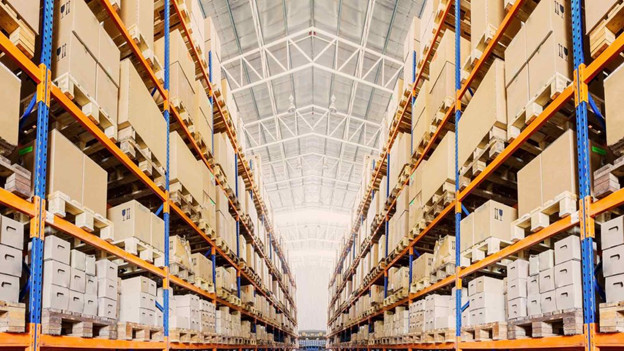
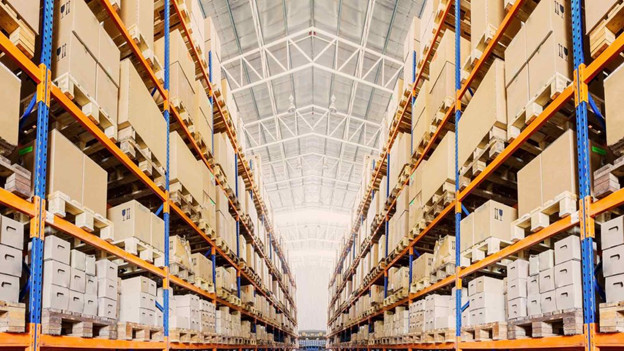
Before many businesses sell or distribute their goods, they store the items in an on-site or off-site warehouse. Businesses handle their warehousing needs in a variety of ways. They can choose to store stock in their own storage spaces or in a rented warehouse. The stock is organized and controlled by in-house staff or third-party warehousing companies. Many warehousing tasks are automated using the software while other processes are still handled manually by human staff.
When companies hire third-party companies, they are provided with more than just warehouses for rent. Warehousing companies offer a range of services that ensure the safety of the goods on their premises, while also managing incoming stock, picking, packing, and shipping orders correctly. A major consideration in this region is the warehouse air temperature. With high seasonal temperatures, a professional warehouse setup will include strict temperature controls to avoid heat damage to goods. When all of these processes occur efficiently, a company saves on its overheads and in turn, increases its profits.
What does warehouse management involve?
In simple terms, warehouse management refers to all the processes involved in the effective day-to-day management of the inventory and equipment in a warehouse. When a company rents a warehouse, they can expect the facility to handle the following processes for them:
- Inbound processing – in which goods are received by the warehouse, checked and documented, before being stored away in their assigned location on the site. Sometimes, inefficient warehouse facilities, goods are packed and immediately dispatched to the customer without a requirement for storage.
- Warehouse layout and slotting – in which goods are organized into categories and placed accordingly. Generally speaking, high-demand, fast-moving goods are assigned locations close to the front of the warehouse. Goods that tend to be bought together are stored in spaces near to each other. Similar goods that can be mistaken for each other should be placed well away from each other.
- Picking – in which goods are placed in an organized system so the packers can quickly and conveniently locate them.
- Packing – in which workers pack goods according to their corresponding packing protocol, which includes the provision of a content slip and delivery manifest.
- Shipping – in which workers carefully move packed orders from their storage space to the assigned freight vehicle promptly.
- Managing returns – in which returned goods are unloaded, checked off against the original order, and logged against the customer’s account.
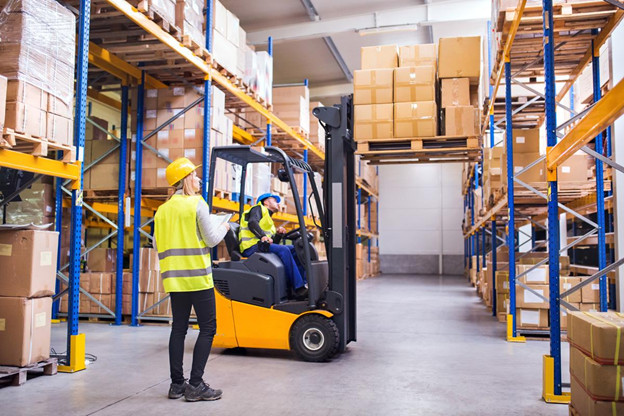
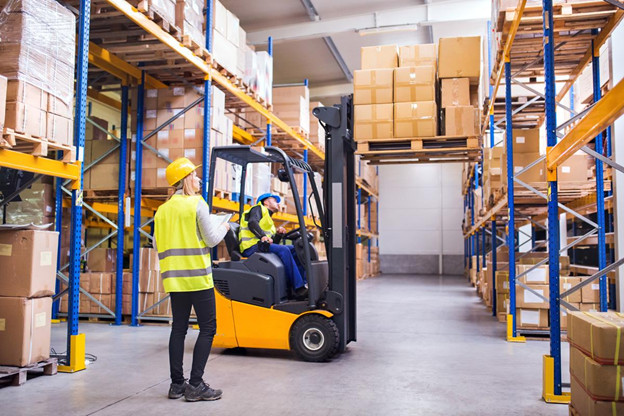
Many businesses, particularly those operating on a large scale, also hire warehousing companies for the more targeted services they offer:
Inventory management
One of the most important services provided by a warehousing company is inventory management. Effective inventory management means that goods are ordered, stored, and dispatched in a way that ensures the business always has a sufficient supply of goods.
There are different models of inventory management. Two of the most popular ones are just in time and ABC analysis. With just-in-time inventory management, goods are scheduled to arrive precisely when they are forecast to be required. In ABC analysis, goods are sorted and allotted storage space based on their consumption value, with category A goods being high-value items that are stocked in the highest amounts and category C goods being low-value items that are stocked in the least amounts.
Outsourcing inventory management to storage experts frees up managers and business owners for other core business activities. When a dedicated, reliable warehouse team manages inventory effectively, a business will not lose sales due to low inventory or waste capital due to excess stock taking up the available storage space.
Some companies also opt for the drop-shipping model, where goods are directly transferred from their manufacturing site to the customers with no intermediary stop at a warehouse at all. These businesses are not likely to rent a warehouse.
Cross-docking
Cross-docking is another inventory management strategy involving the direct transfer of goods from the manufacturer to the consumer. However, unlike drop shipping, the goods do actually arrive at a warehouse but are directly loaded into outgoing freight vehicles and dispatched to the customer.
This is a popular strategy with businesses that produce perishable goods, in-demand products, high-quality items that do not require additional warehouse inspection, and promotional or new-to-market goods. When businesses exclusively use cross-docking as a means of goods transfer, it’s possible they may not need a warehouse for rent.
Cross-docking is beneficial for companies because it saves both time, costs, and space by eliminating the need for warehouse workers to sort, store and pack the items. However, it comes with the risk of creating discrepancies in inventory control as the items are never transferred to a warehouse for logging. Additional processes need to be incorporated into the standard inventory management system for cross-docking items to enter the system.
Palletization
Palletization is a time-saving practice at warehouses where individual items are placed on a wooden base called a pallet, allowing multiple goods to be stored, handled, and transported simultaneously. Compared to lose cargo, palletized goods are loaded and unloaded faster, resulting in the faster turnaround of freight vehicles and greater overall transport efficiency. Palletized handling and storage also allows for the warehouse to be available for subsequent shipments faster.
It also has several other operational benefits, including a reduction in labor costs and a lower chance of injury to goods and workers.
One drawback of palletization is the challenge of allocating adequate storage space for empty pallets, which take up substantial room in a warehouse when they are not in use. Most warehousing companies, however, offer storage space solutions for idle pallets.
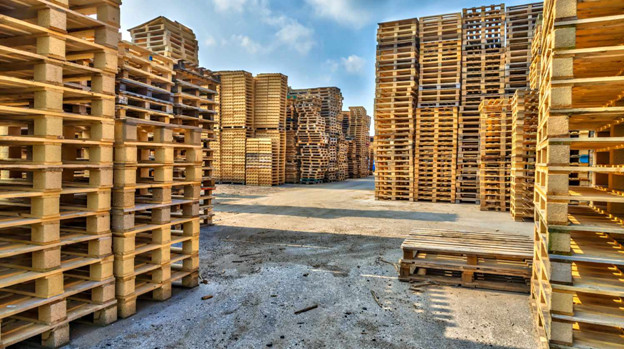
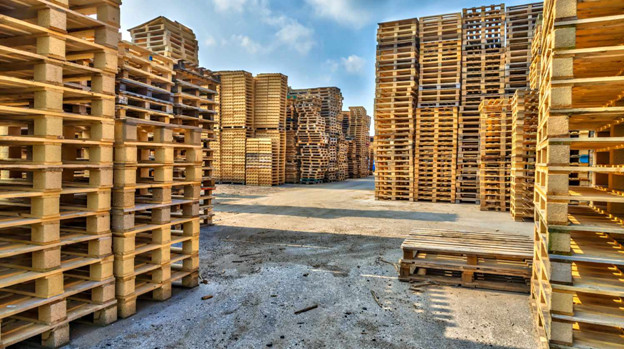
Empty pallet provision
Warehouses that use palletized handling methods should also employ best practices for allocating safe and efficient storage space for unused pallets. Depending on whether pallets are being stored indoors or outdoors, there are some general rules to follow to ensure that they do not pose a fire or toppling hazard.
When stored inside, pallets must be stacked vertically, that is, stored with their broad horizontal base on the ground. In other words, pallets can’t be stacked on their sides to save storage space, as that would increase their chances of falling over and causing harm to workers and damage to property.
It is also necessary for pallets to be stored away from flammable materials, gas sources as well as other storage spaces to reduce the extent of damage in the event of a fire. It’s also recommended for damaged pallets to be disposed of immediately.
When being placed in outdoor storage space, pallets need to be covered with a tarp to protect them from weather damage, especially in areas with high temperatures such as Saudi Arabia and the Middle East in general. There are protocols provided by insurance companies that limit the number of pallets that can be stored outside.
Shrink and stretch wrapping
In order to protect items stored and moved on pallets, warehousing companies offer shrink wrapping and stretch wrapping facilities.
Both wrapping methods involve the use of highly resistant plastic film to envelop the pallets and use different means to accomplish this. Shrinkwrapping uses heat to shrink and tighten plastic wrap around a product. It is commonly used to preserve food and beverages during shipping.
Stretch wrapping uses a turntable platform to spin a unit load while a machine or hand-powered mechanism wraps plastic around it. Machine wrap is more commonly used for large loads and in high-volume warehouses, while the opposite is true for hand wrap.
By shrink or stretch wrapping pallets, warehouse companies prevent damage to goods through mishandling or movement during transportation. It also protects the unit load from being discolored by dust and dirt or weakened by moisture.
Labeling
Although it sounds like a basic process, labeling is one of the most crucial functions that warehouse companies serve for businesses. Without a proper labeling system, products can be considered as good as lost in a warehouse’s numerous storage spaces. This is often the case when overburdened or undertrained staff are in charge of organizing stock at a company warehouse.
Professional warehouse companies have highly trained staff and a stringent labeling protocol that maximizes handling efficiency and guarantees accurate order delivery for their clients. Once an item enters a warehouse, it is continually identified as it passes through various stages of the storage process. Moreover, the various storage spaces of the warehouse are also labeled, along with any rules or regulations that need to be followed to maintain a safe work environment.
Inspection
Before goods are shipped to customers from warehouses, warehouse companies perform a quality inspection to guarantee that the product did not suffer damage in the storage space. Some products are sensitive to environmental conditions and changes in temperature or moisture can cause them to deteriorate. Regular inspections in the warehouse ensure that goods are still in a viable condition for shipping to customers.